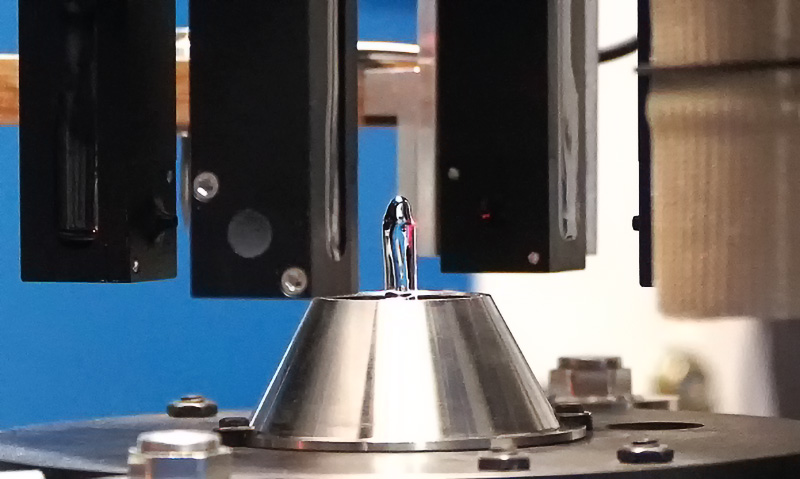
automatische Wellenhöhenregelung im Miniwellen-Lötprozess.
Innerhalb einstellbarer Toleranzen wird die Wellenhöhe basierend auf den Messergebnissen und einem mathematischen Modell automatisch nachgeregelt, indem die Parameter entsprechend verändert werden.
Bewegen sich die erforderlichen Einstellungen außerhalb des definierten Toleranzbereichs, errechnet das System eine Empfehlung, jedoch entscheidet der Maschinenbediener oder der Prozessverantwortliche, ob die Parameteranpassungen zur Regelung der Wellenhöhe übernommen werden, oder ob zunächst die Ursache gegebenenfalls an anderer Stelle zu suchen ist. Alle Messergebnisse und nachgeregelten Parameter werden für eine vollständige Nachvollziehbarkeit des Prozesses protokolliert, so dass gleichzeitig auch ein Qualitätsnachweis für die hergestellten Produkte zur Verfügung steht.
Die Vorteile liegen hier auf der Hand: Die frühzeitige Erkennung von Prozessabweichungen ermöglicht die schnelle Analyse und Behebung der Ursache, sichert die Produktqualität und senkt nachhaltig die Fertigungskosten durch die Vermeidung von Nacharbeit.
Im Selektivlötprozess, wo naturgemäß mit sehr kleinen Lötdüsengeometrien gearbeitet wird, ist die Wellenhöhe natürlich ebenfalls ein kritischer Faktor.
Bei Multidüsen-Prozessen ist die Wellenhöhenüberwachung mit Wirbelstromsensor ein effektives Kontrollwerkzeug. Basierend auf dem Prinzip der kommunizierenden Röhren, einer indirekten Messung, entsteht hierbei sowohl an den Lötdüsen als auch am Messtrichter die gleiche Höhe und wird über das Signal des Wirbelstromsensors konstant geregelt.
Das einfachste Verfahren bei Miniwellen-Prozessen besteht in der Verwendung einer Messnadel, die mit der Spitze eine Kontaktmessung zur Lötwellenoberfläche ausführt. Alternativ kann die Wellenhöhe mit einem Lasermesssystem automatisch geregelt werden. Die Messung findet hierbei simultan zum Produktionsprozess statt, so dass die Taktzeit nicht beeinflusst wird.
Besonders effektiv ist der von SEHO entwickelte Kreuzsensor, der gleich mehrere Funktionen übernimmt. Zum einen wird hiermit die Wellenhöhe in Miniwellen-Lötprozessen präzise geregelt. Gleichzeitig dient der Kreuzsensor aber auch zur automatischen Werkzeugvermessung: Durchmesser, Höhe und Einbaulage der Lötdüse werden automatisch geprüft und somit potenzielle Bedienfehler ausgeschlossen.
Im Hinblick auf die Stabilität der Wellenhöhe bietet auch die neue LongLife Miniwellen-Lötdüse einen besonderen Vorteil. Bedingt durch das spezielle Herstellungsverfahren verfügt diese Lötdüse über eine sehr gleichmäßige Düsenwandung. Hierdurch wird die Wellenhöhe konstant stabil gehalten, so dass insgesamt eine höhere Prozessstabilität und geringere Lötfehlerraten gewährleistet sind. Bei schlecht aktivierten Düsen kann sich der Mittelpunkt verschieben, wodurch Lötbrücken entstehen oder SMD-Bauteile abgeschwemmt werden können. Aufgrund ihrer Materialeigenschaften ist die LongLife-Lötdüse dagegen nahezu durchgängig perfekt aktiviert.
Zusätzliche automatische Überwachungsfunktionen, speziell bei Selektivlötanlagen, tragen dazu bei, potenzielle Lötfehler zu vermeiden. Hierzu gehören zum Beispiel die automatische Korrektur der x, y und z-Werte bei Baugruppen mit Versatz oder Durchbiegung, oder ein intelligentes Tool-Management, bei dem über Sensoren und Software überwacht wird, dass nur Produkte zur Bearbeitung eingelassen werden, für die die Anlage entsprechend gerüstet ist. Auch die kontinuierliche automatische Überwachung der Stickstoff-Eingangsqualität sowie der für den Prozess erforderlichen Stickstoffmenge trägt zur Sicherung reproduzierbarer Ergebnisse entscheidend bei.
Gesicherte Ergebnisse
100% Prozesskontrolle sichert das THT-AOI-System PowerVision von SEHO, das je nach Anforderung als Modul vor einer Lötanlage in die Fertigungslinie integriert werden kann und auf Bestückbandebene mit einer automatischen Bestückkontrolle ausgestattet ist, so dass fehlerhaft bestückte Baugruppen gar nicht erst gelötet werden. Im Rücktransport, d.h. im unteren Anlagenbereich, kann eine automatische Lötstelleninspektion integriert werden, die gelötete Baugruppen auf typische Lötfehler wie beispielsweise unvollständige Lötstellen, Menisken oder Lotperlen kontrolliert. Applikationsabhängig kann das AOI-System aber auch direkt in eine Selektiv-Lötanlage von SEHO integriert werden, was im Hinblick auf die Gesamtproduktionslinie enorme Vorteile bietet. Generell ist die volle Integration des Systems und der Prüfergebnisse in die Hard- und Softwarearchitektur der SEHO-Lötanlagen gewährleistet und die Auswertung von Trend- und Serienfehlermeldungen ermöglicht eine frühzeitige Prozessoptimierung, wodurch die Effizienz der Fertigungslinie deutlich gesteigert wird. Dies betrifft besonders die Bauteilebestückung und den Lötprozess, aber auch Designfehler werden schnell sichtbar.
Fazit
Automatische Kontrollfunktionen können Elektronikhersteller effektiv dabei unterstützen, ihre Fertigungsprozesse nachhaltig stabil und kosteneffizient zu gestalten. Die Basis bilden eine kontinuierliche Erfassung von Maschinen- und Prozessdaten, der bidirektionaler Datenaustausch zwischen den Anlagen, die Möglichkeit der Steuerung durch übergeordnete Systeme und natürlich clevere Ideen der Anlagenhersteller.
SEHO Systems GmbH I Frankenstr. 7 – 11 I 97892 Kreuzwertheim I ( +49 (0) 93 42 / 889-0 I info@seho.de | www.seho.de