Heike Schlessmann & Arne Neiser, SEHO, Kreuzwertheim
Elektronikfertigungen stehen mehr denn je vor Herausforderungen, wenn sie in einem wettbewerbsintensiven Umfeld erfolgreich sein möchten. Einerseits dominiert die Vorgabe einer konstant hohen Qualität der hergestellten Produkte, die häufig eine gewisse Flexibilität in den Herstellungsprozessen voraussetzt. Auf der anderen Seite Preisdruck und insgesamt das Ziel, die Fertigungsprozesse nachhaltiger zu gestalten, um für die Zukunft gut aufgestellt zu sein. Die Minimierung von Materialabfällen, der ökonomische und ökologische Einsatz von Ressourcen und die Vermeidung potenzieller Lötfehler stehen im Fokus.
Bei der Transformation zur nachhaltigen Elektronikfertigung können Maschinenhersteller effektiv unterstützen. Energie- und ressourceneffizientere Anlagen, die Erhöhung der Flexibilität des Fertigungsequipments, um wirtschaftlich auf Produktionsschwankungen reagieren zu können, höhere Automatisierungsgrade bei der Prozesskontrolle, um mögliche Lötfehler zu vermeiden und natürlich die Optimierung der Gesamtkostenstruktur sind einige der Ansatzpunkte. Häufig sind es schon die kleinen Dinge, die einen Unterschied machen.
Abfall vermeiden
Wenn es darum geht, die Entstehung von Abfall in Wellenlötprozessen zu minimieren lohnt es sich, über eine Stickstoffatmosphäre nachzudenken. Je weniger Sauerstoff im Prozess vorhanden ist, desto niedriger ist die Oxidbildung im Lötbad, und was nicht in Form von Oxiden als „Abfall“ entfernt werden muss, muss folglich nicht als frisches Lot wieder zugeführt werden. Rund 30 kg Oxide, die im 3-Schicht-Betrieb in einer offenen Anlage entstehen, reduzieren sich so auf bis nur 5 kg in einer Stickstoff-Tunnelanlage. Gleichzeitig ist auch die Maschinenverfügbarkeit deutlich höher, da der Reinigungsaufwand ebenfalls verringert wird.
Auch auf den Flussmittelverbrauch hat eine Stickstoffatmosphäre einen positiven Einfluss. Die Hauptaufgabe des Flussmittels besteht darin, Oxid- und Polymerschichten von den Metalloberflächen zu entfernen und vor einer neuen Oxidation zu schützen. Ein Großteil des Flussmittels wird beim Durchlaufen der 1. Welle abgewaschen, die Lötverbindung entsteht aber direkt nach Durchlaufen der 2. Welle und das Abziehverhalten ist entscheidend für ihre Form. Inerte Bedingungen sorgen für verbesserte Benetzungseigenschaften und eine geringere Oberflächenspannung des flüssigen Lots. Die Reoxidation der metallisierten Oberflächen wird verhindert und die „on-top-Menge“ an Flussmittel, die zur Entfernung von Metalloxiden in einer Umgebungsatmosphäre erforderlich ist, kann in einer Stickstoffatmosphäre eingespart werden.
Durch die Verwendung von Stickstoff in Lötprozessen entstehen zunächst natürlich auch Kosten, was direkt zu der Frage führt, wie der Stickstoffverbrauch auf das minimal erforderliche Maß reduziert werden kann.
Moderne Anlagen können mit einer automatischen Regelung ausgestattet werden, die für eine konstant stabile Stickstoffatmosphäre sorgt und verhindert, dass der N2-Verbrauch, beispielsweise aufgrund von unsymmetrischen Strömungen im Tunnel, unbemerkt abdriftet.
Auch smarte Funktionen, wie zum Beispiel ein ECO-Mode, tragen dazu bei, einen nachhaltigeren Lötprozess kosteneffizient umzusetzen und ermöglichen Einsparungen von bis zu 20 %. Mit dem ECO-Mode wird die Stickstoffzufuhr automatisch gedrosselt, wenn aktuell keine Baugruppen zur Bearbeitung anstehen. Abhängig von den individuellen Fertigungsanforderungen kann eine Anlage so programmiert werden, dass sie nach x Minuten Inaktivität automatisch die N2-Zufuhr reduziert, oder beispielsweise nur zu festen Pausenzeiten.
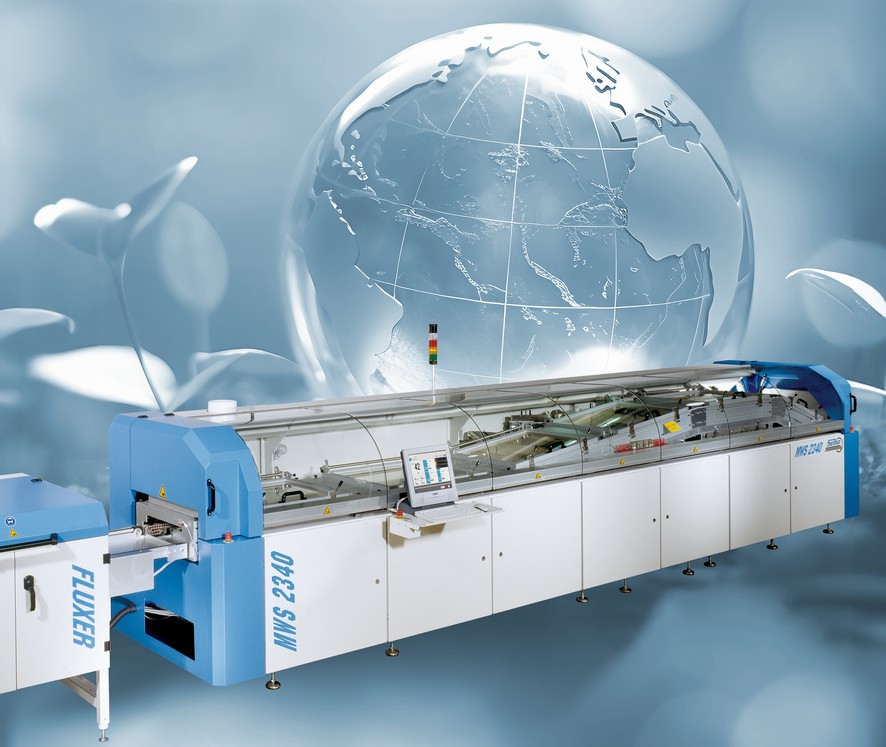
Potenziale nutzen
Deutliche Ressourceneinsparungen sind im Fluxerbereich möglich, unabhängig davon, ob die Wellenlötanlage in einer Stickstoffatmosphäre betrieben wird oder nicht.
Ein moderner Sprühkopf sorgt bei stabilem Sprühstrahl für eine höhere Ausnutzung des Flussmittels. Es entstehen weniger Sprühnebel, wodurch der Verschmutzungsgrad in der Anlage minimiert wird. Dadurch ergibt sich eine Kostenersparnis von beiden Seiten. Allein der Flussmittelverbrauch kann durch einen modernen HVLP-Sprühkopf (High Volume – Low Pressure) im Vergleich zu einem normalen Sprühkopf um bis zu 30 % reduziert werden.
Mit der Überwachung der aufgetragenen Flussmittelmenge ergibt sich ein weiteres Potenzial für Einsparungen: Abweichungen vom Sollwert werden sehr früh festgestellt und die Ursache, wie zum Beispiel Verschmutzungen oder Ablagerungen, defekte Schläuche oder Verschleiß, kann schnell behoben werden. Die häufig eingestellte „Reservemenge“ beim Flussmittelauftrag kann entfallen.
Üblicherweise wird in Wellenlötprozessen das Flussmittel auf der gesamten Baugruppe aufgetragen, auch dann, wenn nicht in allen Bereichen tatsächlich gelötet wird. Mit der smarten Funktion des segmentierten Flussmittelauftrags ist es möglich, nur die Baugruppenbereiche zu fluxen, in denen sich Lötstellen befinden. Bis zu acht verschiedene Bereiche können innerhalb einer Baugruppe definiert werden, jedes Segment mit einer Größe von minimal 50 x 50 mm. Abhängig vom Baugruppenlayout kann das Einsparpotenzial schnell bei 50 % und mehr liegen.
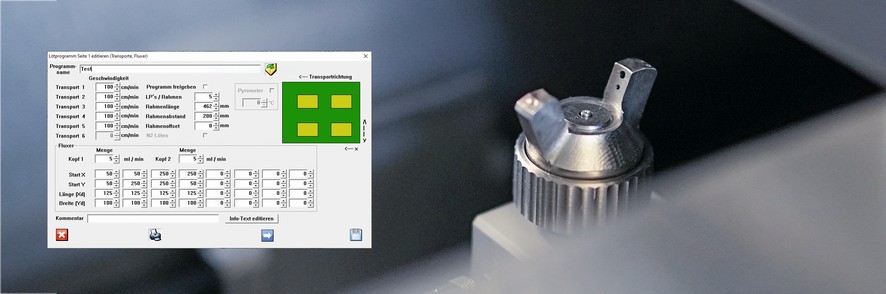
Löten = Wärme und Wärme = Energie
Das weitaus größte Potenzial für Einsparungen bietet der Sektor Energie und hier gibt es gleich mehrere Ansatzpunkte.
Beim Aufheizen einer Lötanlage treten in aller Regel Lastspitzen auf, die einen hohen Energiebedarf haben. Entsprechend hoch ist das Einsparpotenzial, wenn diese Lastspitzen vermieden werden. Mit einem ECO-Mode werden die Vorheizungen bis zur vollständigen Betriebsbereitschaft der Anlage zeitlich getrennt voneinander angesteuert. Durch diesen optimierten Aufheizmodus kann der Energiebedarf um bis zu 30 % gesenkt werden.
Rund 70 % des Energieverbrauchs einer Wellenlötanlage wird für den Vorheizprozess benötigt. Eine Anlage mit einer Gesamtanschlussleistung von 38 kW, ausgestattet mit Infrarot- und Quarzstrahlern im Vorheizbereich, regelt sich im Betrieb bei einem durchschnittlichen Verbrauch von ca. 14 kW ein. Wird die Vorheizung ausgeschaltet, sinkt der Energieverbrauch bei gleichbleibender Lötbadtemperatur von 260°C auf ca. 4 kW.
Von der Prozessseite her kann auf das Vorheizen der Baugruppen nicht verzichtet werden. Im Umkehrschluss braucht man also Lösungen, um bei mindestens konstanter Produktionsleistung den Energiebedarf im Vorheizprozess zu reduzieren.
Bei der Ermittlung der Energieeffizienz einer Lötanlage spielen mehrere Maschinenzustände eine Rolle:
• Ausgeschaltet: Kein Energieverbrauch, aber es dauert eine gewisse Zeit, bis die Anlage wieder einsatzbereit ist.
• Standby: Die Maschine benötigt nur eine kurze Zeit, um wieder im Bereitschaftszustand zu sein.
• Variable Last: Es laufen weniger Produkte in die Anlage ein, als sie verarbeiten könnte.
• 100 % Last: Die Maschine produziert mit maximalem Durchsatz.
Werfen wir nun zunächst einen Blick auf drei unterschiedliche Strahlertypen. Quarzstrahler sind im Lötprozess eine gängige Vorheizmethode, erreichen aber nur eine mittlere Heizeffizienz von 60-70 %, metallummantelte Strahler sogar noch weniger. Pulsarstrahler geben mehr als 85 % der gesamten Leistung in Infrarotwärme ab, sind also deutlich effektiver. Davon abgesehen sind sie innerhalb weniger Sekunden auf voller Leistung, während andere Strahlertypen eine gewisse Anlaufzeit benötigen.
Betrachtet man den Wellenbereich, in dem die verschiedenen Strahlertypen arbeiten, befinden sich Pulsarstrahler im mittleren Wellenbereich. Sie haben also eine höhere Eindringtiefe als Quarzstrahler, wodurch sie bei der Wärmeübertragung effizienter sind.
Im Vergleich zu Quarzstrahlern sind mit Pulsarstrahlern daher Einsparungen von bis zu 10 % möglich. In Relation zu Infrarotheizungen werden durch gezieltes Takten Energieeinsparungen von bis zu 30 % erreicht.
Pulsarstrahler verfügen im Vergleich zu Quarzstrahlern also über eine höhere Heizeffizienz, eine kürzere Reaktionszeit und einen besseren Wärmeeintrag in das Produkt.
Bezieht man die schon erwähnten unterschiedlichen Maschinenzustände mit ein, kann mit Pulsarstrahlern der Energiebedarf der Lötanlage deutlich gesenkt werden. Ist die Maschine leer und in den Standby-Modus gewechselt, können die Heizungen auf ein Minimum gesetzt werden, da es nur Sekunden dauert, bis die Heizleistung wieder innerhalb des Arbeitsbereichs ist. Um die Umgebungsbedingungen in der Anlage konstant zu halten, werden nur ca. 3,5 kW benötigt.
Beträgt das Produktionsvolumen weniger als 100 %, können alle Strahler, über denen sich aktuell kein Produkt befindet, in ihre Standby-Einstellung geschaltet werden. Mit einer geringen Last ist also auch direkt ein niedrigerer Energieverbrauch verbunden. Bei niedriger Maschinenauslastung bis zu 50 % allein durch die Minimierung des Standby-Verbrauchs.
Bei 100 % Last ist die Leistungsaufnahme der Anlage nahezu identisch mit der Leistungsaufnahme einer Maschine mit herkömmlichen Strahlern.
Einer der Hauptvorteile von Pulsarstrahlern ist die schnelle Reguliergeschwindigkeit. Sowohl in der Serie, als auch im Produktmix mit unterschiedlichen thermischen Anforderungen, ist keine Wartezeit zwischen den Produkten erforderlich. Durch die Schaltung von einzelnen Strahlern anstelle von ganzen Heizsegmenten sind kürzeste Baugruppenabstände möglich. In der Praxis bedeutet das, dass jeder einzelne Strahler unterhalb eines Produkts mit den individuell dafür benötigten Einstellungen betrieben werden kann und zum Erreichen dieses individuellen Einstellwertes ist kein zusätzlicher Abstand zwischen verschiedenen Produkten nötig. Im Ergebnis schafft dies eine enorm hohe Flexibilität und maximalen Durchsatz.
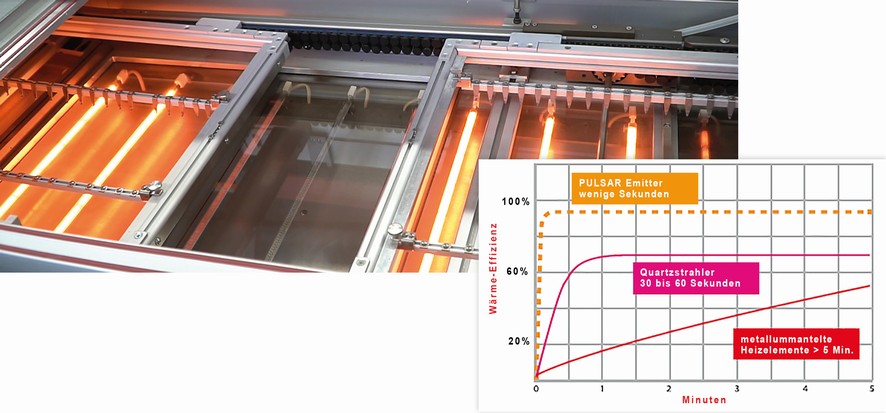
Lötfehler vermeiden
Lötfehler sind nicht nur ärgerlich, sondern vor allem zeitintensiv und kostspielig. Im besten Fall erfordern sie zusätzliche Prozessschritte und Nacharbeit, und dadurch auch einen unnötigen Einsatz von Energie, Materialien und Personal. Im schlimmsten Fall ist das Produkt Ausschuss.
Zu den häufigsten Lötfehlern gehören Fehler aufgrund schlechter Benetzung, vor allem dann, wenn das Baugruppen- oder Maskenlayout anspruchsvoll ist. Je nach Maskenstärke und Größe der Maskenausschnitte ist eine sichere Benetzung aller Lötstellen nicht immer gewährleistet. Zusätzlich können geringe Abstände zwischen den abgedeckten Bauelementen und den Pins der zu lötenden Bauteile zur Herausforderung werden. Unvollständige Lötstellen, fehlende Durchstiege oder auch Lötbrücken sind dann klassische Fehler.
Smarte Funktionen wie die automatische Düsenhöhenverstellung sind eine innovative Herangehensweise für solche Herausforderungen. Die Lötdüsen sind hier einzeln und softwaregesteuert über eine Distanz von 20 mm verstellbar, um produktabhängig immer den optimalen Abstand zwischen Leiterplatte und Lötdüse zu haben, und zwar in bis zu 16 verschiedenen Abschnitten einer Leiterplatte.
Der gesamte Prozess wird dadurch unabhängig vom Werkstückträger- oder Baugruppendesign, ohne Einfluss auf die Taktzeit. Alle Lötstellen können zuverlässig benetzt werden, wodurch das Risiko von Lötfehlern drastisch reduziert wird. Gleichzeitig bietet die automatische Düsenhöhenverstellung maximale Flexibilität und sichert so die Zukunftsfähigkeit der Wellenlötanlage im Hinblick auf neue Applikationen.
Auch die stabile Höhe der Lötwelle ist prozessrelevant. Schlechte Durchstiege oder fehlende bzw. ungenügende Benetzung können die Folge einer unregelmäßigen Wellenhöhe sein, weshalb sie in Selektiv-Lötprozessen seit langem automatisch überwacht und geregelt wird.
Es gibt durchaus auch Verfahren für Wellenlötprozesse, die allerdings alle mit Einschränkungen verbunden sind: Die Wellenhöhe wird nicht über die gesamte Breite gemessen, die Produktion muss unterbrochen werden oder es sind keine Rückschlüsse auf die individuelle Fertigung möglich.
Mit dem Fokus auf genau diesem Aspekt hat SEHO die automatische Wellenhöhenmessung entwickelt. Das System basiert auf einer Kontaktmessung über die gesamte Wellenbreite, die sowohl bei laminaren als auch bei turbulenten Lötwellen zuverlässige Ergebnisse und Prozesse sichert, und die Taktzeit der Wellenlötanlage nicht beeinflusst.
Um den Idealzustand der Wellenhöhe zu bestimmen, wird zunächst eine Referenzmessung durchgeführt. Im Produktionsmodus erfolgen dann in einem programmierbaren Zeitraster automatisch Messungen der Wellenhöhe. Basierend auf diesen Messergebnissen und einem mathematischen Modell wird die Wellenhöhe innerhalb einstellbarer Toleranzen automatisch nachgeregelt. Alle Messergebnisse und nachgeregelten Parameter werden für die vollständige Nachvollziehbarkeit natürlich dokumentiert.
Die Vorteile liegen auf der Hand: Prozessabweichungen werden früh erkannt und die Ursache kann schnell analysiert und behoben werden. Dadurch ist eine hohe Produktqualität sichergestellt und durch die Vermeidung von Nacharbeit oder Ausschuss werden die Fertigungskosten nachhaltig gesenkt.
Lötfehler sind nicht nur ärgerlich, sondern vor allem zeitintensiv und kostspielig. Im besten Fall erfordern sie zusätzliche Prozessschritte und Nacharbeit, und dadurch auch einen unnötigen Einsatz von Energie, Materialien und Personal. Im schlimmsten Fall ist das Produkt Ausschuss.
Zu den häufigsten Lötfehlern gehören Fehler aufgrund schlechter Benetzung, vor allem dann, wenn das Baugruppen- oder Maskenlayout anspruchsvoll ist. Je nach Maskenstärke und Größe der Maskenausschnitte ist eine sichere Benetzung aller Lötstellen nicht immer gewährleistet. Zusätzlich können geringe Abstände zwischen den abgedeckten Bauelementen und den Pins der zu lötenden Bauteile zur Herausforderung werden. Unvollständige Lötstellen, fehlende Durchstiege oder auch Lötbrücken sind dann klassische Fehler.
Smarte Funktionen wie die automatische Düsenhöhenverstellung sind eine innovative Herangehensweise für solche Herausforderungen. Die Lötdüsen sind hier einzeln und softwaregesteuert über eine Distanz von 20 mm verstellbar, um produktabhängig immer den optimalen Abstand zwischen Leiterplatte und Lötdüse zu haben, und zwar in bis zu 16 verschiedenen Abschnitten einer Leiterplatte.
Der gesamte Prozess wird dadurch unabhängig vom Werkstückträger- oder Baugruppendesign, ohne Einfluss auf die Taktzeit. Alle Lötstellen können zuverlässig benetzt werden, wodurch das Risiko von Lötfehlern drastisch reduziert wird. Gleichzeitig bietet die automatische Düsenhöhenverstellung maximale Flexibilität und sichert so die Zukunftsfähigkeit der Wellenlötanlage im Hinblick auf neue Applikationen.
Auch die stabile Höhe der Lötwelle ist prozessrelevant. Schlechte Durchstiege oder fehlende bzw. ungenügende Benetzung können die Folge einer unregelmäßigen Wellenhöhe sein, weshalb sie in Selektiv-Lötprozessen seit langem automatisch überwacht und geregelt wird.
Es gibt durchaus auch Verfahren für Wellenlötprozesse, die allerdings alle mit Einschränkungen verbunden sind: Die Wellenhöhe wird nicht über die gesamte Breite gemessen, die Produktion muss unterbrochen werden oder es sind keine Rückschlüsse auf die individuelle Fertigung möglich.
Mit dem Fokus auf genau diesem Aspekt hat SEHO die automatische Wellenhöhenmessung entwickelt. Das System basiert auf einer Kontaktmessung über die gesamte Wellenbreite, die sowohl bei laminaren als auch bei turbulenten Lötwellen zuverlässige Ergebnisse und Prozesse sichert, und die Taktzeit der Wellenlötanlage nicht beeinflusst.
Um den Idealzustand der Wellenhöhe zu bestimmen, wird zunächst eine Referenzmessung durchgeführt. Im Produktionsmodus erfolgen dann in einem programmierbaren Zeitraster automatisch Messungen der Wellenhöhe. Basierend auf diesen Messergebnissen und einem mathematischen Modell wird die Wellenhöhe innerhalb einstellbarer Toleranzen automatisch nachgeregelt. Alle Messergebnisse und nachgeregelten Parameter werden für die vollständige Nachvollziehbarkeit natürlich dokumentiert.
Die Vorteile liegen auf der Hand: Prozessabweichungen werden früh erkannt und die Ursache kann schnell analysiert und behoben werden. Dadurch ist eine hohe Produktqualität sichergestellt und durch die Vermeidung von Nacharbeit oder Ausschuss werden die Fertigungskosten nachhaltig gesenkt.
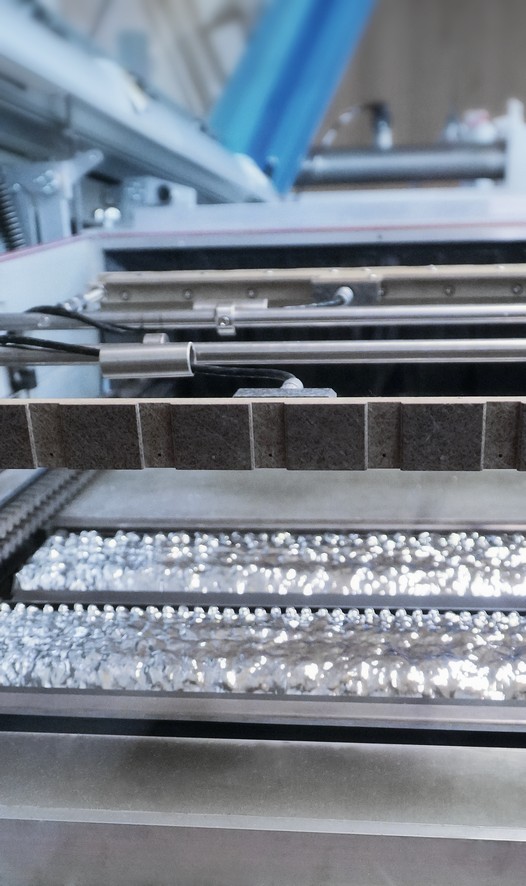
Fazit
Die Fertigung elektronischer Produkte für die Zukunft nachhaltiger zu gestalten, gehört heute zu den primären Zielen. Durch Modernisierung und smarte Maschinenfunktionen werden nicht nur die Energie- und Ressourceneffizienz gesteigert, sondern auch umweltfreundlichere Produktionsprozesse ermöglicht. Mit der richtigen Strategie kann die moderne, nachhaltige Ausrichtung des Lötprozesses zu einer langfristigen Kostenoptimierung führen und dabei den ökologischen Fußabdruck minimieren
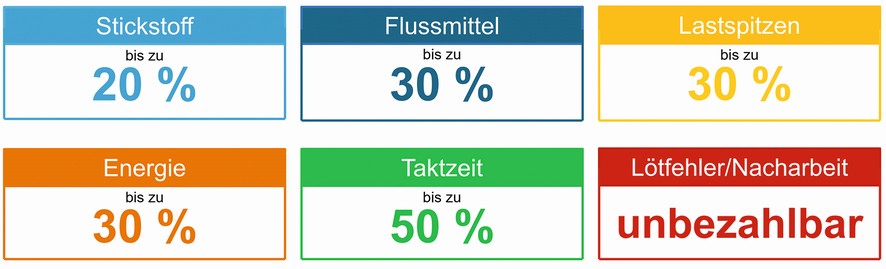