Die Lösung des Produktivitätsparadoxons
von Michael Ford, Sr. Director Emerging Industry Strategy, Aegis Software
Eigentlich sollte man meinen, dass unsere deutschen Freunde nach einigen Jahren Erfahrung mit Industrie 4.0, nun die Früchte des Erfolgs ernten würden, den Industrie 4.0 mit sich bringt. Jüngste Studien belegen allerdings, dass die gesamtwirtschaftliche Produktivität in deutschen Fabriken de facto zurückgegangen ist, obwohl Investitionen in neue Automatisierungstechnologien getätigt worden sind.
Der gängige Begriff hierfür lautet “Produktivitätsparadoxon”.
In Fachkreisen ist diese Entwicklung allerdings keine große Überraschung, da bloße Investitionen in die Automatisierung lediglich eine Erweiterung von Industrie 3.0 bedeuten. Die wahre Bedeutung von Industrie 4.0 ist bisher verkannt geblieben, die den Fabrikbetrieb zunächst von Grund auf ändert, ehe dann die intelligenten Technologien und KI-Tools (künstliche Intelligenz) ihre Arbeit effektiv aufnehmen können.
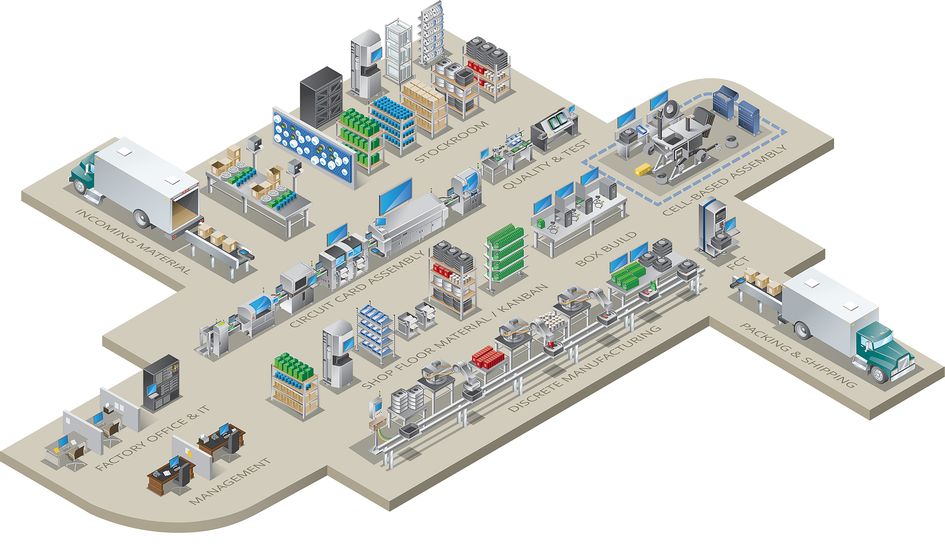
Der Fokus einer MES-Lösung liegt primär in der Fähigkeit, den geplanten Produktionsfortschritt und die damit verbundenen Aktivitäten
zu verfolgen, um diesen Plan dann an Veränderungen der Kundennachfrage, den verfügbaren Materialien und der Prozessfähigkeit anzupassen.
In der Welt der Elektronikfertigung erleben wir ein Worst-Case Szenario der Auswirkungen von Veränderungen auf den Produktionsbetrieb. Wir haben verinnerlicht, dass ein höherer Produktmix eine geringere Produktivität zur Folge hat. Natürlich kann man argumentieren, dass das Geschäft das einfach so mit sich bringt, wenn man in einer Branche tätig ist, in der Flexibilität verlangt wird, ohne dass man jedoch einen erhöhten Lagerbestand mit fertiggestellten Produkten aufweisen möchte. Das ist jedoch nur eine sehr einseitige Erklärung, denn SMT-Maschinenhersteller haben ihre Anlagen bereits seit langem mit Hard- und Software basierten Lösungen an eine flexible Produktion angepasst. Förderer können beispielsweise überall auf den Maschinen platziert werden, es gibt Techniken, die schnelle Rüstwechsel mit gemeinsamer Fördererkonfiguration für Gruppen ähnlicher Produkte ermöglichen. Selbst Rüstwechsel zwischen unterschiedlichen Produkten können durch einen simplen Austausch von Wechseltischen durchgeführt werden. Selbst ohne diese technologischen Hilfsmittel variiert die manuelle Rüstzeit an einer voll beladenen SMT-Bestückmaschine von Unternehmen zu Unternehmen zwischen fünf Minuten und sechs Stunden, je nachdem, welchen Ansatz das Unternehmen verfolgt. Wenn Sie wissen möchten, wie man den SMT Rüstwechsel in nur fünf Minuten erreichen kann, dann müssen Sie sich den Boxenstopp bei einem Formel-1-Rennen zum Vorbild nehmen. Große Verluste einzufahren, nur um Flexibilität zu erreichen, sind keineswegs einfach hinzunehmen, denn es stehen ausreichend technologische Optionen zur Verfügung, die dem entgegenwirken können.
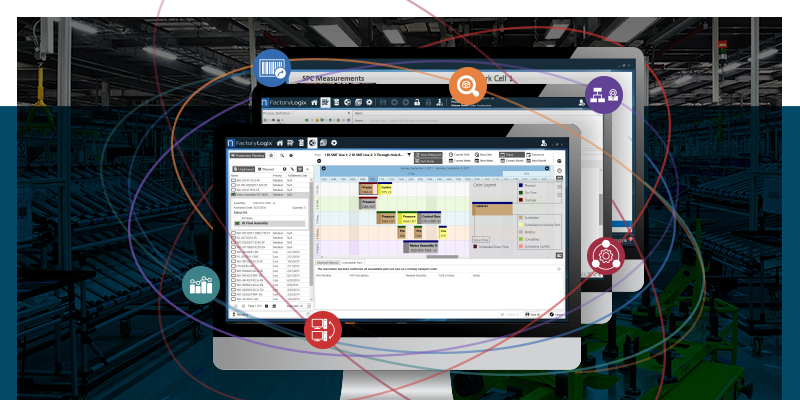
Alle Funktionen zur Fertigungsunterstützung in einem System zusammengeführt- Das ist
einfacher, effizienter und spart Kosten. FactoryLogix liefert Paperless, Qualität, Traceability
und Prozessüberprüfung über ein benutzerkonfiguriertes Interface. Der gesamte Umfang
dieser Funktionen zur Unterstützung der Linienbediener war früher mit kostspieligen
Anpassungen verbunden. All das kommt nun Out-of-the-Box.
Ungeachtet dessen wächst und gedeiht das “Produktivitätsparadoxon” trotzdem. Erst vor kurzem habe ich bei einer Veranstaltung in Skandinavien gezeigt, wie hohe Produktivitätserwartungen von 80% im heutigen High-Mix Umfeld durch nur noch 20% bis 40% ersetzt werden. Hinterher sprach mich ein Teilnehmer darauf an, da er der Meinung war, ich hätte meine Zahlen durcheinandergebracht. Denn sein Unternehmen könnte von 20% nur träumen. Der tatsächliche Prozentsatz ist in vielen Unternehmen heutzutage sogar noch wesentlich geringer. Diese Aussage schient die deutsche Studie zu stützen. Der Produktmix in der Produktion nimmt bei gleichzeitig volatiler Nachfrage immer weiter zu, da die Kunden sowohl Liefermenge als auch Lieferzeiten zwar ad hoc ändern können möchten aber gleichzeitig nicht bereit sind, zusätzliche Lagerkosten für Pufferbestände zu tragen. Die Fabriken zahlen den Preis für die Auswirkungen dieser schwankenden Kundennachfrage direkt in ihre automatisierten Produktionslinien.
Wenn man aus diesem Dilemma einen Ausweg finden möchte, muss man sich einmal anschauen, was in Bezug auf Metriken in Fabriken überhaupt berichtet wird. Die gesetzten Ziele sind der entscheidende Faktor für die Fertigungsleistung. Es werden Berichte und Diagramme erstellt, die die Ziele genau festlegen und die Erfolge definieren, wie beispielsweise rechtzeitige Lieferung, Produktionsrate, Materialausschuss, Qualitätsprobleme usw. In gewisser Weise wird jeder, der in der Fabrik tätig ist, an diesen Statistiken gemessen. Das Management möchte, dass sämtliche Prozesse unter Kontrolle sind und stetig Verbesserungen vorgenommen werden. In Anbetracht der Tatsache, welche Devisen in den Fabriken ausgerufen werden, erscheint der Fokus auf die Produktivitätsperspektive schon fast optimistisch verglichen mit dem, was man angesichts des Produktivitätsparadoxons erwarten würde. Jedes nur halbwegs mathematisch begabte Kind würde sehr schnell zu dem Ergebnis kommen, dass die Metriken in der Fabrik auf einem anderen Datensatz beruhen als die deutsche Studie. Und genau hier liegt das Problem.
Interne Leistungen können zu Recht auf vielfältige Art und Weise gemessen werden. Es können Statistiken erhoben werden, um darzustellen, welche bestimmte Perspektive benötigt wird. Diese Art der Berichterstattung kam auf, als Massenproduktionen gang und gäbe waren. Spezielle Produktionslinien stellten Produkte so schnell wie möglich her. Der Schwerpunkt lag damals ganz klar darauf, immer höheren Durchsatz mit jedem Quadratmeter Linienfläche zu erzielen. Die Leistung wurde einfach daran gemessen, wie viel pro Stunde bestückt werden konnten. In die Optimierung von Maschinenprogrammen wurde sehr viel Zeit investiert. Die akkurate Messung der Maschinenleistung bedeutete jedoch, dass Stillstandzeiten der Maschine, die nicht maschinenbedingt erfolgten, einfach ignoriert wurden. Wenn die Linie am Tag potenziell 2.000 Produkte fertigen konnte, dann war das die Zahl anhand derer die Maschinenleistung gemessen wurde. Es war jedoch in höchstem Maße unwahrscheinlich, dass der Kunde pro Tag genau 2.000 Produkte benötigte. Selbst in diesen Tagen gab es bereits eine schwankende Nachfrage. Wenn die Lager vor fertiggestellten Produkten schier überquollen, dann stoppte man außerplanmäßig die Linie und nutzte die Zeit, um „Wartungen“ durchzuführen. Diese Zeiten wurden dann aus der Produktivitätsberechnung herausgenommen, denn aus Sicht der Maschinenbauer handelte es sich hierbei um eine externe, unkontrollierbare Variable. Diese ungünstige Herangehensweise nahm irgendwann immer größere Ausmaße an, weil einfach immer mehr Ausnahmen gemacht wurden, um mit zunehmendem Produktmix bestimmte enge Verantwortungsbereiche widerzuspiegeln. Als dann auch noch Techniken zur Handhabung von High-Mix ins Spiel kamen, wurden die Produktivitäts- und Kapazitätsberechnungen immer schwieriger.
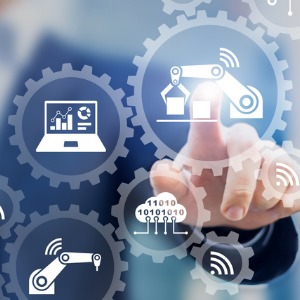
Industry 4.0 bedeutet die Optimierung aller
Aspekte innerhalb eines Fertigungsprozesses
durch die Verwendung von Live-Daten.
So wurde beispielsweise das auftragsübergreifende Rüsten von Förderern bei SMT-Bestückmaschinen als eine Möglichkeit gesehen, physische Ortswechsel von Material an den Maschinen zwischen unterschiedlichen Produkten zu vermeiden. Wenn nacheinander zwei Produkte mit den gleichen Bauteilen gefertigt werden, dann könnte man doch die Materialien gleich auf der Maschine lassen, und sich somit die Zeit sparen, diese zu wechseln. Dies führte leider zu neuen Einschränkungen für die Optimierung von Maschinenprogrammen. Denn so konnte beispielsweise der Weg, den der Bestückkopf zurücklegen muss, um die am häufigsten verwendeten Bauteile zu ihren Besückpositionen zu befördern, nicht weiter durch die Auswahl der Abholspur optimiert werden. Das führte im Ergebnis dazu, dass die Ausführungszeit des Programms sich verlängerte und daher weniger effektiv wurde. Diese Tatsache wurde oftmals einfach ignoriert, da die Optimierung von Maschinenprogrammen nicht mehr so wichtig war, als die Auswirkungen einer High-Mix Produktion eintraten. Jetzt drehte sich plötzlich alles um die Rüstzeiten. Im Laufe der Zeit überstiegen die Verluste in den Programmen häufig die beim Rüstprozess vermiedenen Verluste. Der Produktivitätsverlust auf Grund verminderter Programmeffizienz fand seinen Weg meistens nicht in die Produktivitätsberichte, da die Durchsatzleistung fast immer an der Programmzeit der Maschine gemessen wurde. Nicht sichtbare Verluste wie dieser wurden immer mehr Teil des regulären Produktionsparadigmas in der High-Mix-Produktion.
Die Produktionsplanung ist in weiteres Beispiel für vergeudete Produktivität. Denn es müssen starre Produktionskonfigurationsregeln für die Zuordnung von Produkten bis hin zu Linienkonfigurationen durch Ingenieure befolgt werden, da der Zeitaufwand für die Aufbereitung der Produktdaten enorm ist. Dies schränkt den Optimierungsprozess selbstverständlich erheblich ein. Herkömmliche generische Planungstools sind in dieser Umgebung völlig nutzlos. In der Realität wird die Produktion mit Hilfe von Excel als ein „Just-in-time“ Planungstool geplant und niemand hat Zeit, darüber nachzudenken, ob bessere Produktionszuordnungspläne erstellt werden können. Die Möglichkeiten, die alleine dadurch verloren gehen, steigen auf Grund dieser Probleme weiter an. Viele von ihnen werden gar nicht gemeldet, sondern fallen unter den Tisch, weil der Fokus viel zu sehr auf einzelne Vorgänge gerichtet ist und insgesamt der Überblick fehlt. Die Produktivitätsberichte, die aus einer bestimmten Perspektive heraus erstellt wurden, schauen auf den ersten Blick gut aus und jeder leistet hervorragende Arbeit. Wenn man aber das ganze Bild betrachtet, fällt auf, dass das Gesamtergebnis in die falsche Richtung läuft und genau das ist es, was die deutsche Studie herausgearbeitet hat. Diese Erkenntnis ist gut, denn selbst wenn die Zahlen selbst sehr schlecht sind, gäbe es ohne diese Informationen ja gar nicht die Möglichkeit, Ursachenforschung zu betreiben und geeignete Gegenmaßnahmen einzuleiten. In der Zwischenzeit soll man gerne weiterhin die interne Leistung jedes Elements in der Fertigung mithilfe der aktuellen Metriken und Kennzahlen messen. Das Eine sollte das Andere nicht ersetzen.
Was die deutsche Studie leider nicht anbietet, ist eine Lösung des Problems. Aus herkömmlicher Perspektive ist die Situation komplex und sehr verwirrend und beinhaltet so viele Variablen und Grenzen, die ihre Ursachen oftmals tief in den technischen Details der einzelnen Vorgänge haben. Diese verborgenen Probleme aufzudecken sind, ebenso, wie die Konsequenzen der Gegenmaßnahmen, die ergriffen werden, sehr schwer verständlich. Von einer Quantifizierung einmal ganz zu schweigen. Um das Ganze verstehen zu können, gibt es zwei Hauptpunkte, die angegangen werden müssen. Zuerst muss man die wirklichen Bedürfnisse der Branche verstehen und zwar die aktuellen Bedürfnisse ebenso wie zukünftige Bedürfnisse. Nehmen wir als Beispiel die in Deutschland aktivste Branche, die Automobilindustrie. Der ganze Stolz der deutschen Automobilbranche ist eine Endmontagelinie, die, präzise wie ein Uhrwerk, in einem bestimmten Takt, zuverlässig immer und rechtzeitig Autos liefert. Selbstverständlich ist diese Linie auch völlig flexibel und kann die buchstäblich unendlich vielen Wünsche und Optionen, die Kunden gerne hätten, mühelos handhaben. Das hört sich schon toll an und könnte die überragende Errungenschaft der Automatisierung sein, die auch noch Aktivitäten durch Personen beinhalten. Wenn man sich jetzt aber nicht nur auf die Endmontagelinie konzentriert, dann wird das Problem, das weiterhin besteht, sehr schnell sichtbar. Die Fabrik muss nämlich immer noch sicherstellen, dass die Gesamtnachfrage nach den Fahrzeugen, die jede einzelne Linie produziert, genau den Kundenanforderungen entspricht, damit kein Lager mit fertigem Warenbestand entsteht. An der Linie gibt es keinerlei Spielraum, andere Modelle herzustellen. Vielmehr werden die Sales und Marketing Abteilungen Kampagnen fahren und Incentives ausloben, damit die Nachfrage in der Fabrik konstant bleibt. Ungeachtet dessen muss die Bestellung eines Kunden auch mit einigen Standard-Builds gemischt werden, damit die Linie kontinuierlich läuft und diese werden dann oftmals zu einem Sonderpreis verkauft. Man könnte jetzt davon ausgehen, dass die Auslieferung eines neuen Autos, auch mit eventueller Sonderausstattung, doch recht schnell geht. Denn wir haben ja gesehen, dass ein paar Tage Vorlaufzeit in der Fabrik völlig ausreichend sind. Stattdessen kann es in der Realität mehrere Monate dauern, bis es einmal zu einem Produktionsslot kommt. In dieser Situation neigen die Kunden dann dazu, sich eben woanders nach einem passenden Auto umzusehen. Der Grund für diese übermäßig lange Vorlaufzeit liegt in der Endmontagelinie. Damit hier keine Stillstandzeiten entstehen, muss im Vorfeld bereits eine bestimmte Menge an Bestellungen eingehen. Das ist nötig, um kalkulieren zu können, wie viele Optionen und Konfigurationen für Unterbaugruppen an das Werk geliefert werden sollen, die dann „just-in-time“ gebraucht werden. Die Kosten für die Flexibilität werden somit einfach verlagert. Die Zulieferer für diese Endmontagelinien sind einer variablen und oftmals auch volatilen Produktionsnachfrage ausgesetzt, die sie irgendwie stillen müssen. Die Lieferung hat innerhalb eines festgelegten Zeitfensters zu erfolgen, nicht früher und selbstverständlich auch nicht später. Eine Optimierung der Handlungsabläufe in der Fabrik der Unterbaugruppen, bedeutet für die Branche dann ein Worst-Case Szenario. Sicherheitskritische Baugruppen erfordern ein detailliertes Qualitäts-, Prozess- und Entwicklungsmanagement. Bei einem sehr großen Produktmix und oftmals geringen Fertigungsaufträgen, sind Änderungen im Werksablauf ständig erforderlich und jede neue Konfiguration muss ihrerseits wieder mit den erforderlichen Standards übereinstimmen. Die Vergütung hierfür ist gering, da die Preispolitik in der Automobilindustrie eine heikle Sache ist. Jeder Automobilzulieferer sollte sich dieser Tatsache bewusst sein und für sich ein Produktionsmodell entwickeln, dass diesem Umstand Rechnung trägt und alle versteckten Verluste aufdeckt und angeht. Dies gilt auch für alle Arten und Bereiche der Elektronik- und Montagefertigung. Es ist aber gar nicht so einfach den optimalen Handlungsablauf festzulegen. Industrie 4.0 wurde genau zu dem Zweck entwickelt diesen Paradigmenwechsel für Handlungsabläufe einzuläuten, sozusagen die softwarebasierte „Automatisierungsschicht“ über die zunehmende Anzahl automatisierter Prozesse, wie sie die alte Industrie 3.0 darstellte. Die deutsche Studie sucht nach Industrie 4.0 reifen Ergebnissen, basiert aber noch auf alten Aktivitäten aus dem Zeitalter von Industrie 3.0. Es ist wirklich höchste Zeit, echte Tools im Sinne von Industrie 4.0 zu erstellen. Und hier sind wir bei dem zweiten Hauptpunkt, der angegangen werden muss, angelangt.
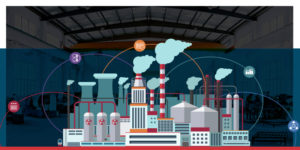
FactoryLogix spart Zeit, vereinfacht Neuanläufe
und beseitigt das NPI-Chaos. Als Komplettpaket
bietet es einen einfachen, schnellen
und gesteuerten NPI-Prozess aus CAD
und BOM.
Industry 4.0 bedeutet die Optimierung aller Aspekte innerhalb eines Fertigungsprozesses durch die Verwendung von Live-Daten. Unabhängig davon, ob es dabei um die Kommunikation der Linien untereinander geht, die Verwaltung schlanker Materialien, eine adaptive Planung und die Zuweisung von Produkten zu Linienkonfigurationen sowie die Entwicklung von Montageverfahren auf Basis eines digitalen Zwillings; die Lösung wird für jedes Unternehmen, dass sich Industrie 4.0 an Bord holt, etwas anders aussehen, je nachdem welches Geschäftsbedürfnis eben vorherrscht. Es ist jedoch nicht praktikabel eine individuelle, maßgeschneiderte Software zu entwickeln, die diese Fabrikprozesse vorantriebt, denn die Preise dafür würden durch die Decke gehen und wäre absolut nicht tragbar. Es muss eine Standardisierung zu einem Grad erfolgen, der die Verwendung von digitalen Standardplattformen unterstützt, die wiederum Werte liefern, die auf der Verwendung von IIOT (Industrial Internet of Things) Technologien speziell für die Fertigung beruhen. Diese Technologie ist der klare Paradigmenwechsel weg von der alten Datenerfassung. Dank der Erfassung des Datenflusses zwischen allen betrieblichen Prozessen, ist ein digitaler und detaillierter ganzheitlicher Blick in Echtzeit auf die Fabrik jederzeit möglich und zwar in einem Umfang, der die gesamte Fertigung und alle damit zusammenhängende Abläufe absolut detailgetreu beinhaltet. Uneingestandene Verluste verschwinden nicht mehr einfach von der Bildfläche und können in jede Aktivität aufgenommen werden, welche die Leistung verbessert, optimiert und betriebliche Entscheidungen trifft, die mit den Zielen von Industrie 4.0 im Einklang stehen. Die Auswirkungen dieser getroffenen Entscheidungen und Veränderungen kann man sehen, messen und immer weiter verfeinern, aber tragen in diesem Fall direkt zur Gesamtproduktivität der Fabrik bei.
Auf der APEX 2018 wurden wir Zeugen der weltweit ersten Demonstration von CFX (Connected Factory Exchange). Obwohl die Kommunikation von Maschinen untereinander an sich nichts Neues ist, hat uns doch die Tatsache, dass Daten von jedem beliebigen Maschinentyp von beliebigen Anbietern auf Abruf von Besuchern auf ihren Handys eingesehen werden konnten und zwar, ohne dass dafür eine bestimmte Software installiert oder konfiguriert werden müsste und wichtige Kennzahlen anzeigt, doch begeistert. Die Einschränkungen, die unterschiedliche Kommunikationsmethoden und unterschiedliche Dateninhalte aus Maschinen mit sich brachten, gehören nun endgültig der Vergangenheit an.
Auf der APEX 2019, nur ein Jahr später, freuen wir uns darauf, den veröffentlichten CFX-Standard in Bezug auf seinen Umfang und seine heutige Kommunikationstiefe in Aktion erleben zu dürfen, der Daten erfasst, die in Dashboards verwendet werden, zur Entscheidungsfindung künstlicher Intelligenz beitragen und die Fabrik optimieren. Unabhängig davon, für welche Software-Tools man sich in der Fertigung entscheidet, so gewährt uns die Fähigkeit, den Status und die Leistung jedes einzelnen Handlungsablaufs in einem Unternehmen einsehen zu können, die Möglichkeit, genau zu erkennen wo Zeit und Geld verloren gehen. Die in der Fabrik eingesetzten Softwaretools können diese Information dann hernehmen und das komplette Unternehmen in Echtzeit optimieren. Maschinenhersteller haben zusätzlich die Möglichkeit viel mehr Daten aus der Umgebung zu erfassen, in der ihre Maschinen arbeiten, denn sie haben Einsicht in Materialien und Planungsinformationen. Mit Hilfe dieser Daten können sie dann ihre maschinellen Abläufe noch weiter automatisch optimieren. Der CFX-Standard, auf den die Branche sich geeinigt hat, wurde entwickelt, um Informationen in allen Bereichen zu liefern, die das Management, die Kontrolle und die Nutzung von Möglichkeiten innerhalb einer Fabrik betreffen. CFX versteht sich als die Definition davon, wie Daten ausgetauscht werden sowie deren Sprache und deren Bedeutung. CFX wird nun in Softwaretools übernommen, die von Maschinenherstellern an der Maschine oder der Linie und den Entscheidungsträgern in der gesamten Fabrik bereitgestellt werden. In der Folge findet ein Paradigmenwechsel auf MES-Eben statt. Ältere MES-Systeme, die Daten einfach erfassen, diese in verschiedenen Datenbanken abspeichern und dann Berichte generieren, werden den Anforderungen, IIoT-Daten in Echtzeit zu verarbeiten, nicht gerecht und stoßen an ihre Grenzen, wenn es um die Themen Live-Optimierung und Unterstützung bei Entscheidungsfindungen geht. Die neue Generation digitaler MES-Systeme, die speziell für eine IIoT/CFX Umgebung entwickelt wurden, bieten hier den größten Nutzen, da sie die gesamte Spannweite sämtlicher Fabrikabläufe umfassen und eine einzige digitale Standardplattform bieten. Sollten maßgeschneiderte Erweiterungen dieser Plattform gewünscht werden, um beispielsweise eine bestimmte Form des Berichtswesens oder Monitoring zu unterstützen und produktspezifische Prozesse, wie Funktionstests, abdecken zu können, ist dies eine leichte Aufgabe für firmeninterne IT-Entwickler, denn sie können die erforderliche CFX-Schnittstelle mit Hilfe des kostenlosen IPC CFX Software Development Kit (SDK) einfach erstellen.
Die Technologien, welche die zahlreichen Anbieter auf der APEX 2019 vorstellen, markieren den Wendepunkt und leiten die Umkehr des Produktivitätsparadoxons ein, denn sie ermöglichen die Etablierung neuer Automatisierungstechniken und digitaler Best Practices, mit deren Hilfe die lang verborgenen, ignorierten und unvermeidlichen Folgen verlorengegangener Produktivität für immer der Vergangenheit angehören werden. Die vollständige Transparenz und Kontrolle auch über die komplexesten Fabrikabläufe wird den Entwicklern und Managern gewährt und bringt den Weitblick, mit dem Ursachen für Verluste bestimmt und beseitigt werden können. Daraus ergibt sich dann wiederum die Möglichkeit für ein erhöhtes Maß an Flexibilität, gesteigerter Produktivität, verbesserter Qualität, pünktlicher Lieferung und einer Reduzierung materialbezogener Kosten. Obwohl die Demonstration von CFX gemeinsam mit dem IPC Hermes Standard (welcher SMEMA ersetzt) bei der APEX 2019 selbstverständlich in ihrem Umfang beschränkt ist, da es sich hierbei um eine nicht zusammenhängende Fertigungslinie handelt, die live auf einem Messebetrieb aktiv ist, werden doch die Grundlagen mehr als deutlich. Branchenexperten werden Ihnen, gemeinsam mit den neuesten CFX-fähigen MES-Softwaretools, erläutern, wie die Anwendung von CFX-Technologie das Produktivitätsparadoxon ein für alle Mal beendet.